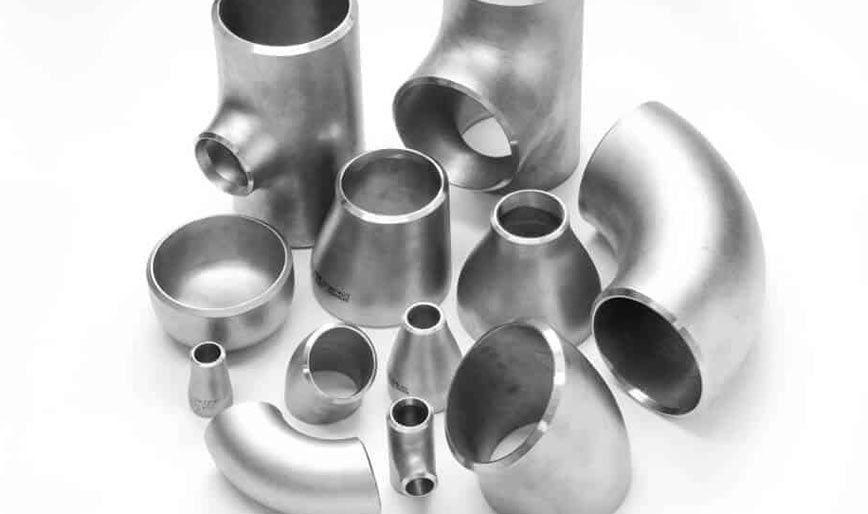
Buttweld Fitting accomplish a lot of admiration by our clients owing to its high strength, dimensional correctness, high tension power, corrosion resistant and consistency. These products are used in various commercial, industrial and automobile industries. We manufacture these fittings using high grade of raw material by implementing most ultra modern technology. These products are clients can avail from us at various sizes, shapes and design as per the requirements.
Buttweld Fittings
Pipe Fittings Specifications | ASTM A403/ ASME SA403 |
---|---|
Pipe Fittings size | Seamless Butt Weld Fittings : 1/2" - 24" Welded Butt Weld Fittings : 1/2" - 24" |
Pipe Fittings Dimensions | ASME/ANSI B16.9, ASME B16.28, MSS-SP-43, BS4504, BS4504, BS1560, BS10 |
Buttweld Fittings Thickness | SCH10, SCH20, SCH30, STD SCH40, SCH60, XS, SCH 80, SCH 100, SCH 120, SCH 140, SCH 160, XXS available with NACE MR 01-75 |
Buttweld Pipe FittingsType | DN15-DN1200 |
ASTM A403 SS Buttweld Fitting Connection | Welding |
Bending Radius | R=1D, 1.5D, 2D, 3D, 5D, 6D, 8D, 10D or Custom ASTM A403 Grade WP Pipe Fitting |
Size Range | ½" NB to 24" NB in Sch 10s, 40s, 80s, 160s, XXS. (DN6~DN100) ASTM A403 WP Buttweld Fitting |
ASTM A403 SS Buttweld Fittings Manufacturing process | Push, Press, Forge, Cast, etc. |
Buttweld Pipe Fittings Test Certificates | EN 10204/3.1B Raw Materials Certificate 100% Radiography Test Report Third Party Inspection Report, etc |
SA 403 Pipe Fittings Origin & Mills | Indian, Japanese, USA, Korean, European, Ukraine, Russian |
Specialized manufacturer of | 90º Elbows, 45º Elbows, Tees, Cross, Reducer, Pipe Cap, Stub End, Pipe Bend |
We provide Material Test Certificates (MTC) as per EN 10204 3.1 and EN 10204 3.2, Test Certificates certifying NACE MR0103, NACE MR0175 |
Manufacturing Standards of Stainless Steel Buttweld Fittings
ASME B16.9 ASTM A403 Pipe Fittings | Factory-Made Wrought Buttwelding Fittings | Long Radius Elbows, Long Radius Reducing Elbows, Long Radius Returns, Short Radius Elbows, Short Radius 180-deg Rerurns, 3D elbows, Straight Tees, Straight Crosses, Reducing Outlet Tees, Reducing Outlet Crosses, Lap Joint Stub Ends, Caps, Reducers |
ASME B16.28 | Short Radius Elbows, Short Radius 180-deg Returns | |
MSS SP43 | Wrought and Fabricated Butt-Welding Fittings for Low Pressure, Corrosion Resistant Applications | Long Radius Elbows, Straight and Reducing-on-the-Outlet Tees, Lap Joint Stub ends, caps, long radius 180 Degree returns, concentric reducers, eccentric reducers |
Mss SP75 | Long Radius Elbows, 3R elbows, straight tees, reducing outlet tees, caps, reducers |
Pipe Fittings has the following advantages :
- Good general corrosion resistance and high strength
- Good sulfide stress corrosion resistance
- Resistance to chloride pitting and crevice corrosion
- Higher resistance to chloride stress corrosion cracking
- Easy to weld and conform
Some of Our Specialities that make us a profitable Business Partner for our clients are :
- Customer focused approach
- Superior quality products
- Timely deliverices
- Customize Size & Specification
- Competitive Pricing
ANSI B16.9 Stainless Steel Buttweld Fittings Forms & Availability
Seamless/ Welded 100% Radiography Tested
Products | Size | |
ASTM A403 SS Elbow – Long Radius | ASTM A403 SS Stub Ends | Sizes 1/2″ – 48″ |
ASTM A403 SS Elbow – Short Radius | ASTM A403 Stainless Steel Cross | |
ASTM A403 Stainless 3D Elbow | ASTM A403 SS 5D Elbow | |
ASTM A403 SS Reducing Elbow | ASTM A403 SS Reducing Cross | |
ASTM A403 Stainless 45° Elbow | ASTM A403 Stainless Tees | |
ASTM A403 SS Fabricated Tee | ASTM A403 Stainless End Cap | |
ASTM A403 Stainless Reducer | ASTM A403 Stainless Coupling | |
ASTM A403 SS Concentric Reducer | ASTM A403 SS Eccentric Reducer | |
ASTM A403 SS Pipe Nipple | ASTM A403 SS Welded Pipe Fittings |
Stainless & Duplex Steel
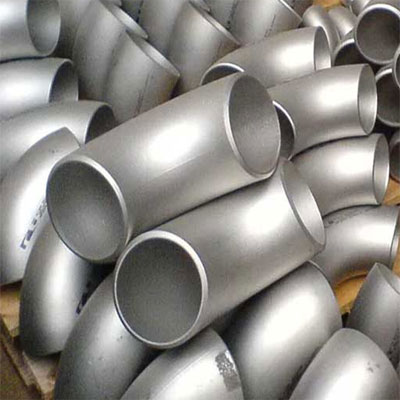
Carbon & Alloy Steel
15 NB UP TO 1200 NB IN SCH 5S , 10S ,10, 20 , 40S , 40 , STD , 60 , 80S , 80 , XS , 100 , 120 , 140 , 160 & XXS.
Form : Seamless & Welded Long Radius & Short Radius Elbow 90 Deg , Long Radius Elbow 45 Deg ,Long Radius & Short Radius Elbow 90 Deg , Long Radius Elbow 45 Deg , Long Radius & Short Radius Elbow 180 Deg ( Return Bend ) , Reducing Elbow , Equal Tee , Un Equal Tee, Crosses , Concentric Reducer , Eccentric Reducer , Long Stubend , Short Stubend , Coller , Pipe Cap , Long Radius Bends R =3 D , 5 D , 6 D , 8 D ,10 D & 20 D In 15 Deg ,30 Deg, 60 Deg & 90 Deg And Drawing Bassed Butt Weld Fitting ( Customised ).
Carbon Steel : ASTM / ASME A 234 WPB , WPC ASTM / ASME A 860 WPHY 42 , WPHY 46 , WPHY 52 , WPH 60 , WPHY 65 & WPHY 70 .
Alloy Steel : ASTM / ASME A 234 WP 1, WP 5, WP 9, WP 11, WP 12, WP 22, WP 23, WP 91
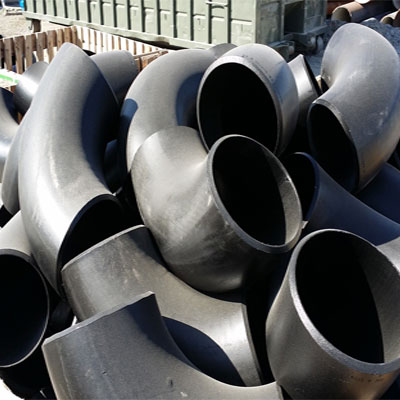
Nickel Alloy
15 NB UP TO 1200 NB IN SCH 5S , 10S ,10, 20 , 40S , 40 , STD , 60 , 80S , 80 , XS , 100 , 120 , 140 , 160 & XXS
Form :Seamless / Erw / Welded in Round & Square .
Nickel Alloy:
ASTM / ASME SB 163 UNS 2200 ( NICKEL 200 )
ASTM / ASME SB 163 UNS 2201 (NICKEL 201 ),
ASTM / ASME SB 163 / 165 UNS 4400 (MONEL 400 )
ASTM / ASME SB 464 UNS 8020 ( ALLOY 20 / 20 CB 3 ),
ASTM / ASME SB 704/705 UNS 8825 INCONEL (825)
ASTM / ASME SB 167 / 517 UNS 6600 (INCONEL 600 )
ASTM / ASME SB 167 UNS 6601 ( INCONEL 601 ),
ASTM / ASME SB 704 /705 UNS 6625 (INCONEL 625)
ASTM / ASME SB 619/622/626 UNS 10276 ( HASTELLOY C 276 )
Copper Alloy :
ASTM / ASME SB 111 UNS NO. C 10100 , 10200 , 10300 , 10800 , 12000,12200, 70600 , 71500 .
ASTM / ASME SB 466 UNS NO. C 70600 ( CU -NI- 90/10) , C 71500 ( CU -NI- 70/30)
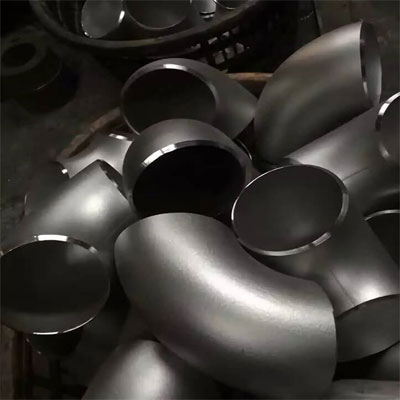
Hastelloy
Standards :ASTM / ASME SB 336 & XXS
Types : Bend (Long & Short)
Elbow (180 Deg., 90 Deg. & 45 Deg.)
Tee (Equal & Unequal)
Reducer (Concentric & Eccentric)
CAP, Stub end (Long &Short)
Nipple (Barrel)
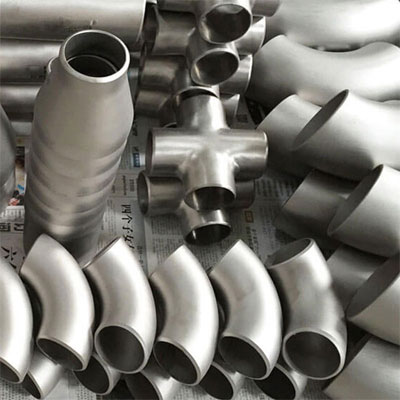
Inconel
Inconel 600, Inconel 601, Inconel 625, Inconel 625LCF, Inconel 686, Inconel 718, Inconel 800, Inconel 825, Inconel X-750
Range : 15 NB UP TO 600 NB IN SCH 5S, 10S,10, 20, 40S, 40, STD, 60, 80S, 80, XS, 100, 120, 140, 160 & XXS
Types : Elbow 90 Deg, Elbow 45 Deg, Elbow 180 Deg, long/short radius elbows, equal/unequal tees, concentric/eccentric reducers, caps, crosses, short/long neck stub-ends
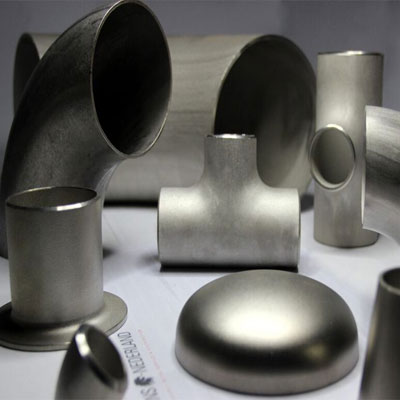
Incoloy
Standards : ASTM B366
Types :
Bend (Long & Short)
Elbow (180 Deg., 90 Deg. & 45 Deg.)
Tee (Equal & Unequal)
Reducer (Concentric & Eccentric)
CAP, Stub end (Long &Short)
Nipple (Barrel)
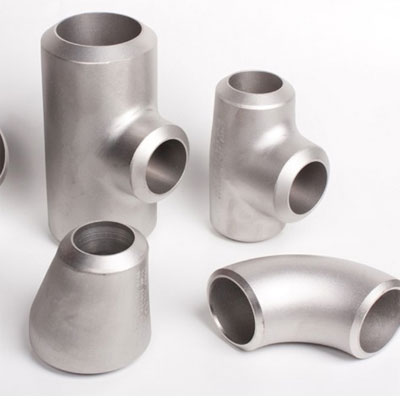
Monel
Range : 1/2" NB to 36" NB
Types : long/short radius elbows, equal/unequal tees, concentric/eccentric reducers, caps, cross, short/long neck stub-ends,
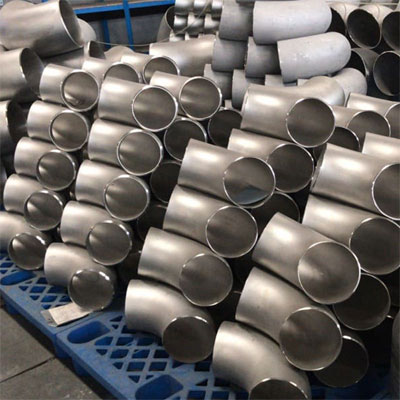
Titanium
Grades : Grade 1, Grade 2, Grade 3, Grade 4, Grade 5,
Grade 7, Grade 9, Grade 23
Range :15 NB To 600 NB in Sch.:5,10,20,40,80,120,160,XS, XXS.
Types :
Bend (Long & Short)
Elbow (180 Deg., 90 Deg. & 45 Deg.) Tee (Equal & Unequal)
Reducer (Concentric & Eccentric)
CAP, Stub end (Long & Short)
Nipple (Barrel)
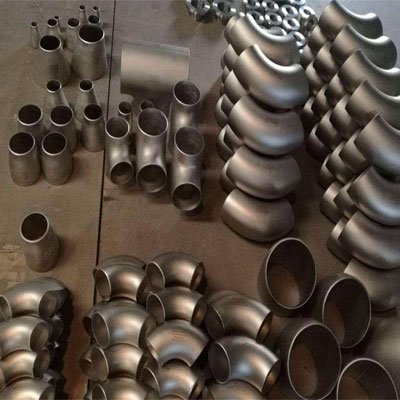
Socketweld & Threaded Fittings
Forged Fitting is high tensile strength, strong, stable, corrosion and rust resistance as well as their high efficiency. We manufacture these forged fittings using premium quality materials in accordance with the quality standards. These products are available in various sizes, shapes and design as per the specific requirements of our clients. Our esteemed clients can avail from us these products at most reasonable prices.
Stainless Steel
|
ASTM A479, A182 - 304, 304L, 304H, 316, 316L, 316H, 316Ti, 309, 310, 317L, 321, 347, 904L, 17-4PH & 400 Series |
---|---|
Mild Steel
|
Gr. 1008, 1010, 1015, 1020, CK35, CK45, CK55, CK60 Etc. |
Carbon Steel
|
ASTM A105, A350 LF2 |
Alloy Steel
|
ASTM A182 F5, F9, F11, F12, F21, F22, F91 |
High Nickel Alloys
|
Hastelloy, Nickel, Monel, Inconel, Incoloy, Alloy-20 & Cupro Nickel |
Non Ferrous
|
Copper |
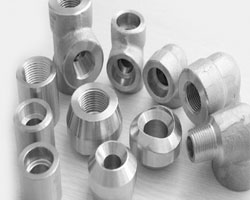
Stainless & Duplex Steel
Range : 15 NB UP TO 100 NB IN 2000 LBS , 3000 LBS , 6000 LBS & 9000 LBS , 150 LBS , 250 LBS.Form :
Socket Weld Fittings : Elbow 90 Deg , Cross , Tee , Elbow 45 Deg , Coupling , Half Coupling & End Cap.
Stainless Steel : ASTM / ASME SA 182 F 304 , 304L , 304H, 309H, 310H , 316 , 316H , 316L , 316 LN , 317 , 317L , 321 , 321H , 347 , 347 H
Duplex Steel: ASTM / ASME SA 182 F 44 , F 45 , F51 , F 53 , F 55 , F 60 , F 61.
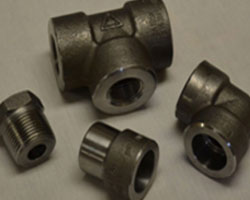
Carbon & Alloy Steel
Range : 15 NB UP TO 100 NB IN 2000 LBS , 3000 LBS , 6000 LBS & 9000 LBS , 150 LBS , 250 LBS.Form : Socket Weld Fittings : Elbow 90 Deg , Cross , Tee , Elbow 45 Deg , Coupling , Half Coupling & End Cap.
Carbon Steel :ASTM / ASME A105.
ASTM / ASME A 350 LF 2 .
Alloy Steel : ASTM / ASME A 182 GR F 5, F 9 , F 11 , F 12 , F 22 , F 91.
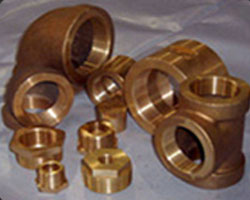
Nickel & Copper Alloy
Range : 15 NB UP TO 100 NB IN 2000 LBS , 3000 LBS , 6000 LBS & 9000 LBS , 150 LBS , 250 LBS.Form :Socket Weld Fittings : Elbow 90 Deg , Cross , Tee , Elbow 45 Deg , Coupling , Half Coupling & End Cap.
Nickel Alloy:
ASTM / ASME SB 564 UNS 2200 ( NICKEL 200 ) ,UNS 4400 (MONEL 400 ) , , UNS 8825 INCONEL (825) , UNS 6600 (INCONEL 600 ) , UNS 6601 ( INCONEL 601 ) , UNS 6625 (INCONEL 625) , UNS 10276 ( HASTELLOY C 276 )
ASTM / ASME SB 160 UNS 2201 (NICKEL 201 ),
ASTM / ASME SB 472 UNS 8020 ( ALLOY 20 / 20 CB 3 ).
Copper Alloy :
ASTM / ASME SB 61 UNS NO. C 92200 & ASTM / ASME SB 62 UNS NO. C 83600.
ASTM / ASME SB 151 UNS NO. 70600 , 71500 , C 70600 ( CU -NI- 90/10) , C 71500 ( CU -NI- 70/30) ,
ASTM / ASME SB 152 UNS NO C 10100 , C 10200 , C 10300 , C 10800 , C 12000, C 12200.
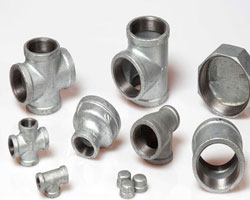
Inconel
Grades : Inconel 600, Inconel 601, Inconel 625, Inconel 625LCF, Inconel 686, Inconel 718, Inconel 800, Inconel 825, Inconel X-750Standard :ASTM / ASME SB 564
Types :Elbows, Equal/Unequal Tees, Concentric/Eccentric Reducers, Full/Half Couplings, Reducing Couplings, Caps, Cross, Unions, Hex/Reducing/Flash Bushings, Plugs, Nipples, Swage Nipples, Reducer Inserts, Boss, Laterals Street Elbows & Outlets/Branch Connections (Weldolets, Thredolets, Sockolets, Flexolets, Latrolets, Elbolets, Sweepolets, Insert Weldolets, Nippolets, Brazolets, Coupolets)
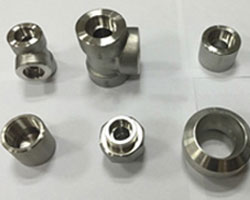
Monel
Grades : Monel 400, Monel k500Types : Elbows, Equal/Unequal Tees, Concentric/Eccentric Reducers, Full/Half Couplings, Reducing Couplings, Caps, Cross, Unions, Hex/Reducing/Flash Bushings, Plugs, Nipples, Swage Nipples, Reducer Inserts, Boss, Laterals Street Elbows & Outlets/Branch Connections (Weldolets, Thredolets, Sockolets, Flexolets, Latrolets, Elbolets, Sweepolets, Insert Weldolets, Nippolets, Brazolets, Coupolets)
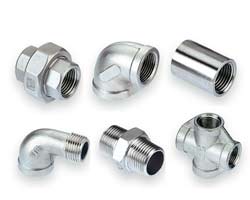
Titanium
Size: 1/2” NB to 4” NBTypes :
Titanium Union
Titanium Coupling
Titanium Full Coupling
Titanium Cross
Titanium Forged Elbow
Titanium Hex Nipple
Titanium Plug
Titanium Bushing
Titanium Boss
Titanium Insert
Titanium Adapter
Titanium Socket
Titanium Forged Tee
Titanium Olets
Titanium Weldolet
Titanium Sockolet
Titanium Elbowlet
Titanium Thredolet
Titanium Nipolet
Titanium Latrolet
Titanium Sweepolet
Titanium Half Coupling
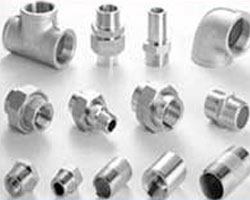
Tantalum
Size: 1/2” NB to 4” NBMaterial : Titanium gr1, gr2, gr5, etc.
Product : Elbow, Tee, Stud End, Reducer
Elbow Type : 45 Deg Elbow, 90 Deg Elbow, 180 Deg Elbow
Tee Type : Straight Tee, Reducing Outlet Tee
Ferrule Fittings
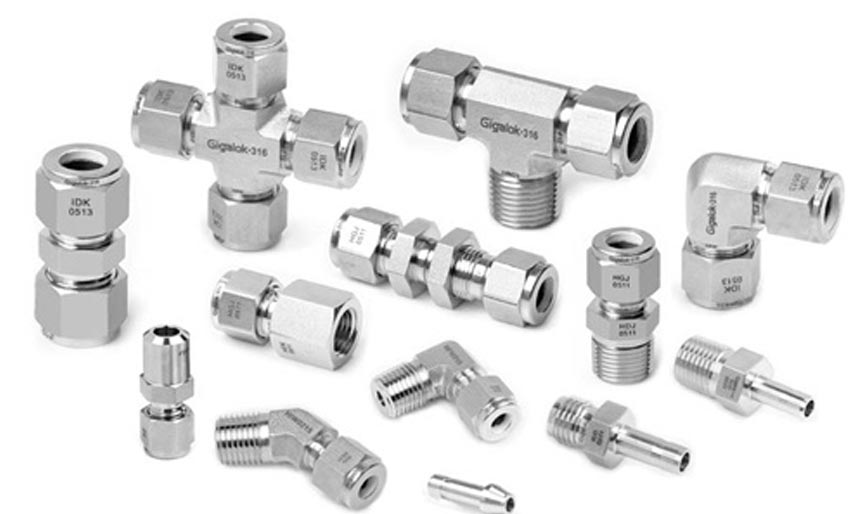
Ferrule fittings are used in various industries, primarily in fluid and gas transfer systems, to provide a secure connection between pipes or tubes. These fittings utilize ferrules, which are small rings or sleeves, to create a tight seal and prevent leakage. They are commonly made from metals like stainless steel, brass, or other alloys, and are valued for their durability and reliability.
Material | Physical Properties | Chemical Properties |
---|
Stainless Steel (e.g., 316) | - Density: 7.98 g/cm³ - Melting Point: 1400-1450°C - Hardness: 200-250 HB |
- Corrosion Resistance: Excellent in most environments - Chemical Resistance: Good against acids, bases, and salts |
Brass (e.g., C36000) | - Density: 8.4 g/cm³ - Melting Point: 900-940°C - Hardness: 120-150 HB |
- Corrosion Resistance: Good in dry air and non-corrosive environments - Chemical Resistance: Limited against acids and ammonia |
Carbon Steel (e.g., ASTM A105) | - Density: 7.85 g/cm³ - Melting Point: 1425-1540°C - Hardness: 180-220 HB |
- Corrosion Resistance: Poor without protective coatings - Chemical Resistance: Limited, susceptible to rust and corrosion |
Physical Properties:
- Density: Mass per unit volume; affects the weight and sturdiness of the fitting.
- Melting Point: Temperature at which the material changes from solid to liquid; relevant for high-temperature applications.
- Hardness: Measure of the material's resistance to deformation; affects durability and wear resistance.
Chemical Properties:
- Corrosion Resistance: Ability to withstand damage caused by reactive substances in the environment.
- Chemical Resistance: Suitability for use in environments exposed to various chemicals, including acids and bases.
Applications:
- Stainless Steel Ferrules: Ideal for harsh environments due to their superior corrosion resistance. Used in chemical processing, marine applications, and high-temperature settings.
- Brass Ferrules: Suitable for general-purpose applications where moderate chemical resistance is adequate. Common in plumbing and hydraulic systems.
- Carbon Steel Ferrules: Often used in applications where cost is a concern and corrosion resistance is less critical. Typically found in low-cost or less corrosive environments.
Dairy Fittings
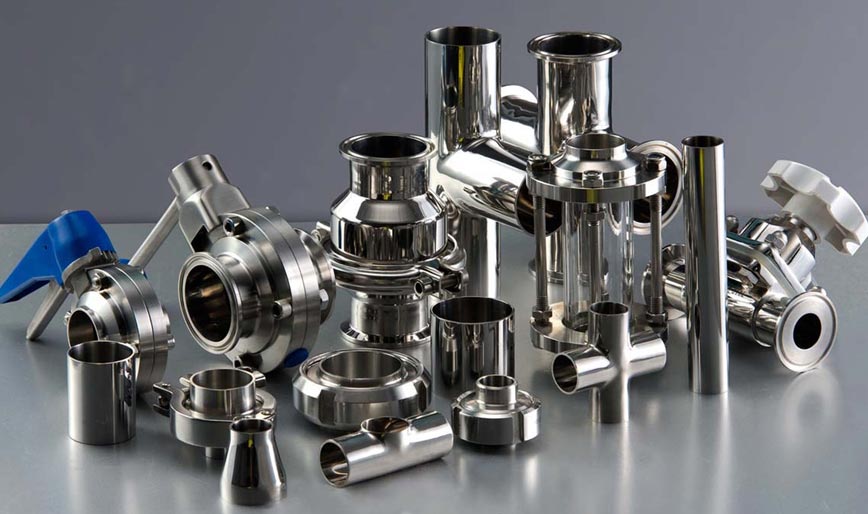
Dairy fittings are crucial components in dairy farming and processing, ensuring efficient and hygienic handling of milk. These fittings typically include:
- Milking Machine Fittings: Components like pulsators, vacuum pumps, and teat cups that are used during the milking process.
- Milk Transfer Systems: Pipes, hoses, and valves that transport milk from the cow to storage tanks or processing areas.
- Cleaning and Sanitizing Equipment: Fittings that help in cleaning and sanitizing the milking equipment and dairy facilities, including cleaning in place (CIP) systems.
- Storage Tank Fittings: Valves, gauges, and connectors that are used with milk storage tanks to ensure proper handling and monitoring.
- Cooling Systems: Fittings related to milk cooling and refrigeration to maintain milk quality and safety.
Property | Physical Properties | Chemical Properties |
---|---|---|
Material | Stainless Steel | Stainless Steel |
Density | 7.7-8.0 g/cm³ | Not applicable |
Melting Point | 1400-1450°C | Not applicable |
Thermal Conductivity | 16-20 W/(m·K) | Not applicable |
Electrical Conductivity | Low, generally non-conductive | Not applicable |
Corrosion Resistance | Excellent in most environments | Resistant to oxidation and most acids |
Tensile Strength | 520-800 MPa | Not applicable |
Hardness | Vickers hardness around 200-250 HV | Not applicable |
Magnetic Properties | Generally non-magnetic (depending on alloy) | Not applicable |
Chemical Stability | Stable in a wide range of pH | Resistant to many chemicals, including acids and alkalis |
Reactivity | Low reactivity with most substances | Resistant to rust and corrosion |
Hygiene | High, easy to clean and sanitize | Non-reactive, does not harbor bacteria |
Hydrolic Fittings
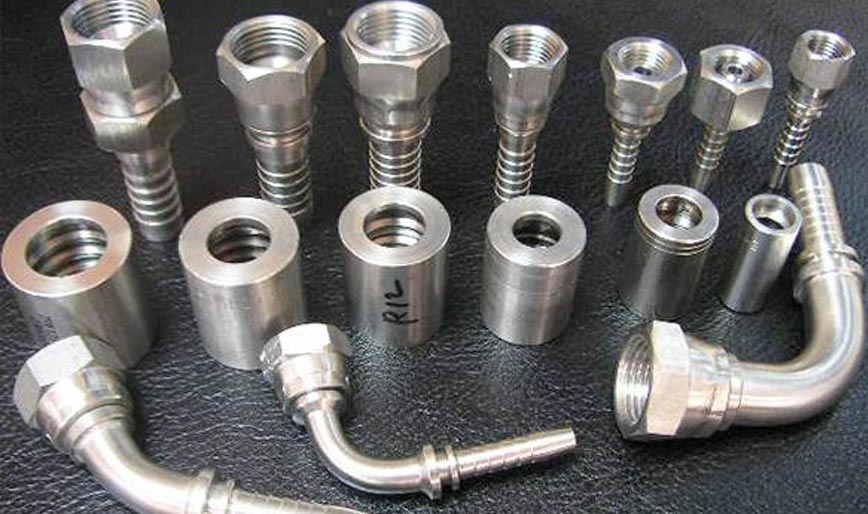
Types of Hydraulic Fittings
-
Threaded Fittings:
- NPT (National Pipe Thread): Tapered threads that form a seal when tightened. Common in general-purpose hydraulic systems.
- BSP (British Standard Pipe): Includes BSPP (Parallel) and BSPT (Tapered). BSPP is used for non-pressure applications, while BSPT is used for high-pressure connections.
-
Flanged Fittings:
- SAE Flange: Includes SAE 4-Bolt and SAE 2-Bolt flanges. Used for high-pressure applications and provide a strong, leak-proof connection.
- DIN Flange: European standard flanges used for high-pressure applications, similar to SAE but with different dimensions and bolt patterns.
-
Couplings:
- Quick Connect/Disconnect: Allows for easy connection and disconnection of hydraulic hoses without the need for tools. Ideal for applications requiring frequent changes.
- Automotive Couplings: Used in automotive hydraulic systems, often featuring a quick-connect mechanism.
-
Adapters:
- Straight Adapters: Connect two hydraulic components in a straight line.
- Elbow Adapters: Change the direction of flow by 90 degrees.
- Tee and Cross Adapters: Allow for branching of hydraulic lines.
-
Compression Fittings:
- Compression Couplings: Used to connect pipes or tubes in a hydraulic system by compressing a fitting around the tube.
Materials Used
-
Steel:
- Carbon Steel: Strong and cost-effective, used in many standard hydraulic applications.
- Alloy Steel: Offers higher strength and resistance to wear and pressure.
-
Stainless Steel:
- Provides excellent corrosion resistance and is used in harsh environments where rust and degradation are concerns.
-
Brass:
- Offers good machinability and corrosion resistance, often used in less aggressive environments.
-
Aluminum:
- Lightweight and resistant to corrosion, used in applications where weight reduction is critical.
Key Properties
-
Pressure Rating: Indicates the maximum pressure a fitting can handle. This is crucial for ensuring the fitting can withstand the operational pressures of the hydraulic system.
-
Temperature Range: Hydraulic fittings must be able to operate within the temperature range of the hydraulic fluid and the operating environment.
-
Corrosion Resistance: Important for fittings exposed to harsh environments or corrosive fluids.
-
Compatibility: Fittings must be compatible with the type of hydraulic fluid used, such as oil or water-based fluids.
-
Sealing: Ensures a leak-proof connection. This can be achieved through various methods, including O-rings, metal-to-metal contact, or thread sealants.
Applications
- Industrial Machinery: Connecting hydraulic components in manufacturing and production machinery.
- Automotive: Used in vehicles for various hydraulic systems like brakes, power steering, and transmission systems.
- Aerospace: Ensuring reliable fluid connections in aircraft hydraulic systems.
- Construction Equipment: Connecting hydraulic components in excavators, loaders, and other heavy machinery.
Maintenance and Safety
- Inspection: Regularly check fittings for signs of wear, corrosion, or damage.
- Torque Specifications: Follow manufacturer recommendations for torque settings to avoid over-tightening or under-tightening.
- Cleaning: Keep fittings and connections clean to prevent contamination of hydraulic fluids.
Property | Steel Fittings | Stainless Steel Fittings | Brass Fittings | Aluminum Fittings |
---|---|---|---|---|
Chemical Composition | Iron, Carbon, Manganese, Chromium (varies) | Iron, Chromium, Nickel | Copper, Zinc | Aluminum, Silicon, Magnesium (varies) |
Density (g/cm³) | ~7.85 | ~8.00 | ~8.4 | ~2.7 |
Tensile Strength (MPa) | 370 - 700 | 520 - 1000 | 210 - 500 | 70 - 500 |
Yield Strength (MPa) | 250 - 500 | 250 - 700 | 150 - 350 | 40 - 300 |
Melting Point (°C) | ~1425 - 1540 | ~1400 - 1450 | ~900 - 940 | ~660 |
Corrosion Resistance | Moderate to Low (depending on coating) | High (resistant to many chemicals and environments) | Moderate (good for low-corrosive environments) | Low (can corrode easily without coating) |
Hardness | 200 - 300 HV (Vickers Hardness) | 200 - 300 HV (Vickers Hardness) | 70 - 150 HV (Vickers Hardness) | 60 - 120 HV (Vickers Hardness) |
Thermal Conductivity (W/m·K) | 50 - 60 | 15 - 30 | 100 - 130 | 200 - 250 |
Electrical Conductivity (S/m) | 1.2 - 1.6 × 10^6 | 1.4 - 2.0 × 10^6 | 1.5 - 1.8 × 10^6 | 3.0 - 4.0 × 10^6 |
Thermal Expansion Coefficient (µm/m·K) | ~11 - 13 | ~16 - 18 | ~19 - 21 | ~23 - 25 |
Other Type Of Fittings
Threaded fittings use internal or external threads to connect hoses, pipes, or tubes.
- NPT (National Pipe Thread): Tapered threads that seal by tightening. Common in the U.S. for general-purpose hydraulic systems.
- BSP (British Standard Pipe): Includes BSPP (Parallel) and BSPT (Tapered). BSPP is for non-pressure applications, and BSPT is used for high-pressure connections.
- JIC (Joint Industry Council): 37-degree flare fittings commonly used in the U.S. for high-pressure hydraulic systems.
- SAE (Society of Automotive Engineers): Includes various types such as SAE 37° Flare, SAE O-Ring Boss (ORB), and SAE Straight Thread.
- UNF (Unified National Fine): Thread used for fine-threaded hydraulic fittings.
- UNC (Unified National Coarse): Coarse-threaded fittings, less common in hydraulic applications.
2. Flanged Fittings
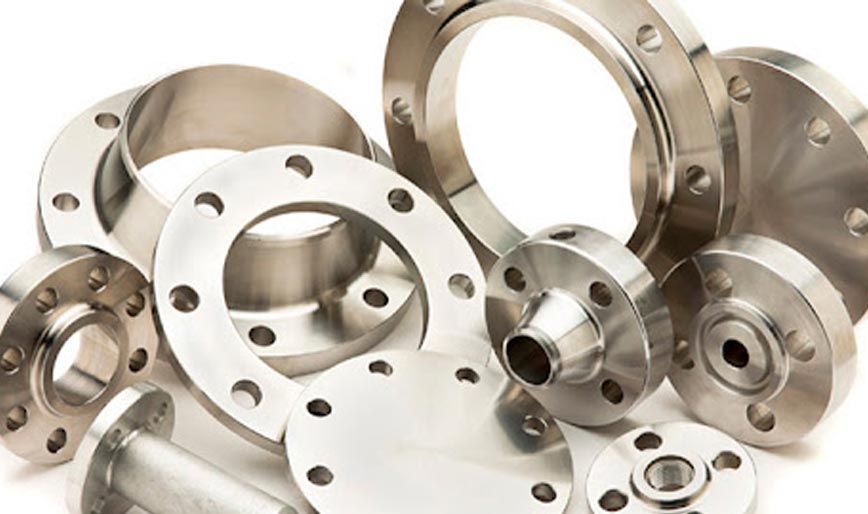
Flanged fittings use a flange to create a strong, leak-proof connection.
- SAE Flange: Includes SAE 4-Bolt and SAE 2-Bolt flanges, used for high-pressure applications.
- DIN Flange: European standard flanges, including DIN 2573 and DIN 2633, used in high-pressure applications with different dimensions and bolt patterns.
3. Couplings
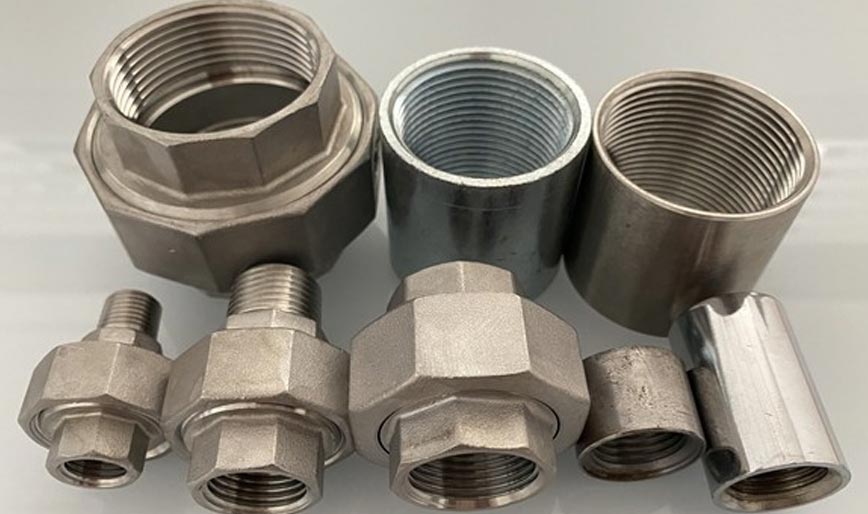
Couplings allow for quick connection and disconnection of hydraulic lines.
- Quick Connect/Disconnect: Provides fast and tool-free connections, suitable for applications requiring frequent changes.
- Automotive Couplings: Used in automotive hydraulic systems with quick-connect mechanisms.
4. Compression Fittings
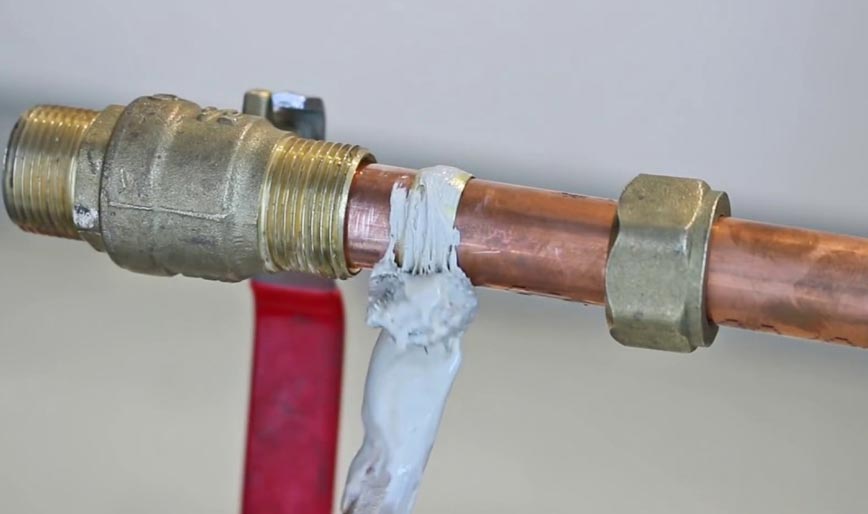
Compression fittings use a compression nut and ferrule to create a seal around the tubing.
- Straight Compression: Connects two pieces of tubing in a straight line.
- Elbow Compression: Changes the direction of flow by 90 degrees.
- Tee Compression: Allows for branching of the hydraulic line.
5. Swivel Fittings
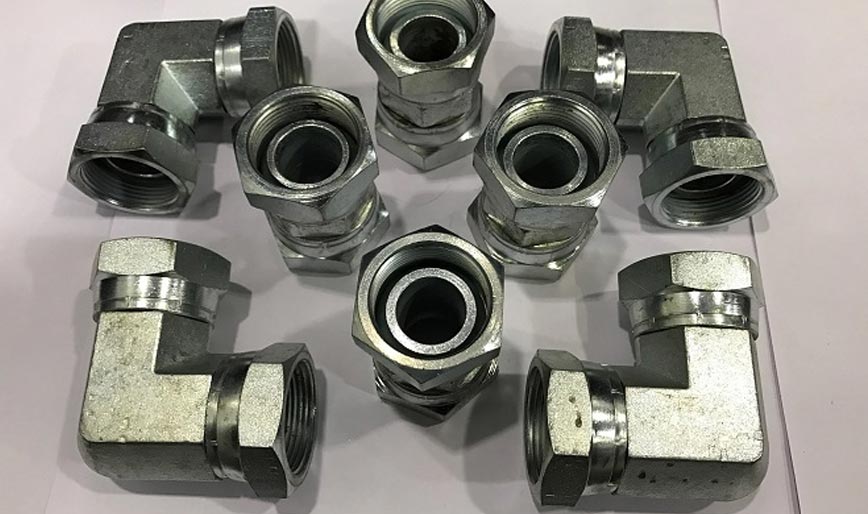
Swivel fittings allow rotation of the fitting while maintaining a secure connection.
- Swivel Elbows: Change the direction of flow while allowing rotational movement.
- Swivel Tees: Provide branching and allow movement to prevent twisting of connected hoses.
6. Banjo Fittings
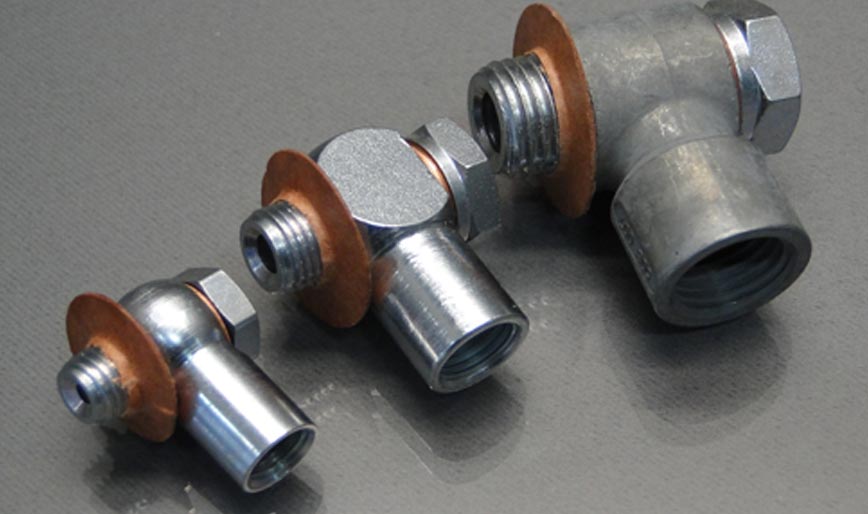
Banjo fittings have a flat, circular flange and a hole in the center to allow fluid flow. Used primarily in automotive and high-pressure applications.
- Banjo Bolt: Used to secure a banjo fitting to a component.
7. Hydraulic Hose Ends
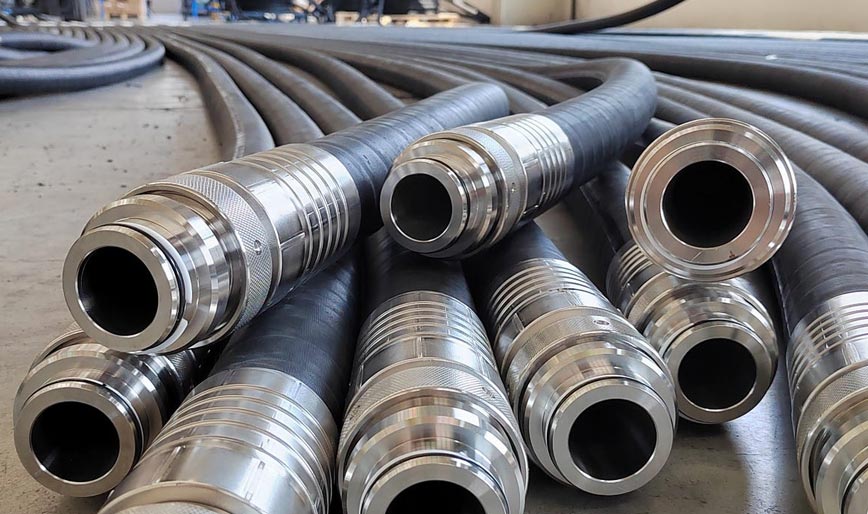
Hydraulic hose ends are designed to attach hoses to fittings or other hydraulic components.
- Crimp Fittings: Fittings that are crimped onto the hose using a hydraulic crimping tool.
- Reusable Hose Ends: Can be removed and reattached to hoses without special tools.
8. Metric Fittings
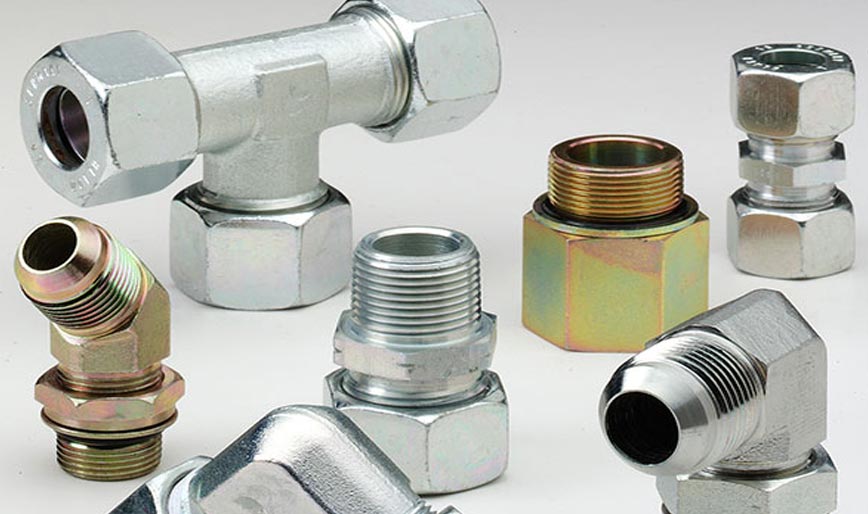
Metric fittings are designed according to international standards and are commonly used in European systems.
- Metric Thread: Includes various thread sizes and types, such as M12, M14, and M16.
9. Push-to-Connect Fittings
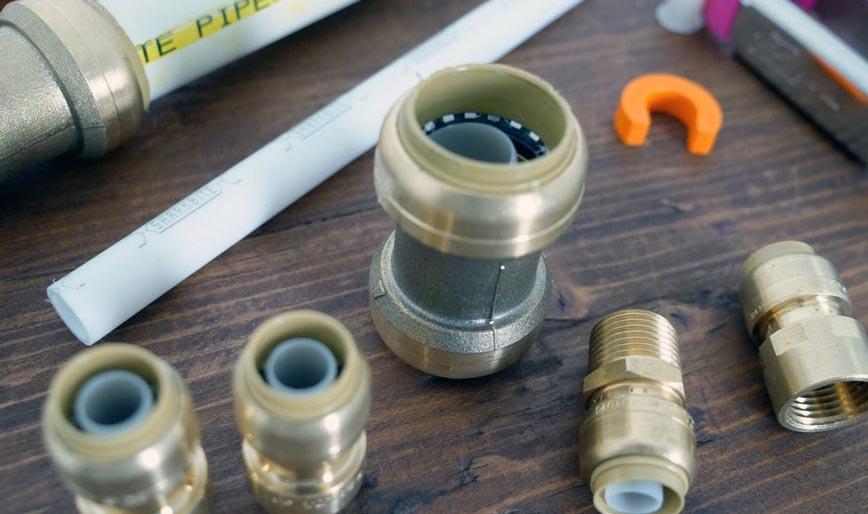
These fittings allow for quick and easy connections without the need for tools.
- Plastic Push-to-Connect: Often used in low-pressure applications and can be easily installed and removed.
- Metal Push-to-Connect: Suitable for higher pressures and more demanding applications.
10. O-Ring Boss (ORB) Fittings
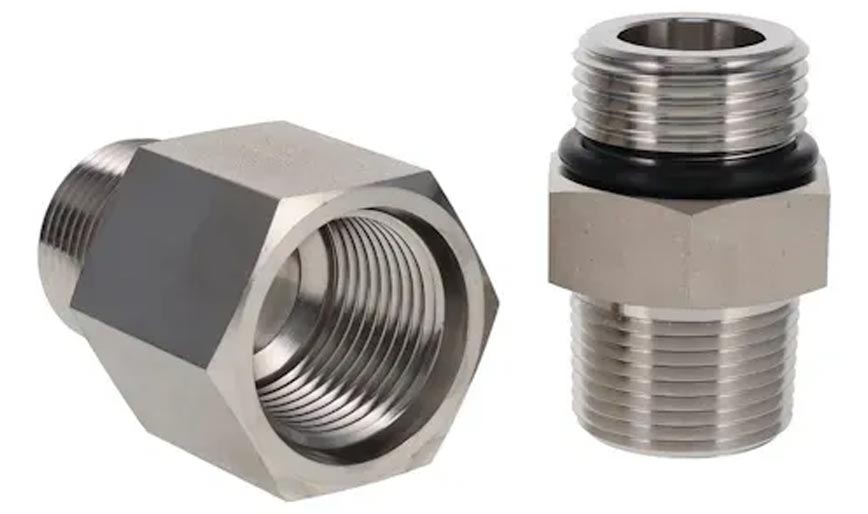
ORB fittings use an O-ring for sealing and are commonly used in hydraulic systems for a reliable and leak-proof connection.
11. Flare Fittings
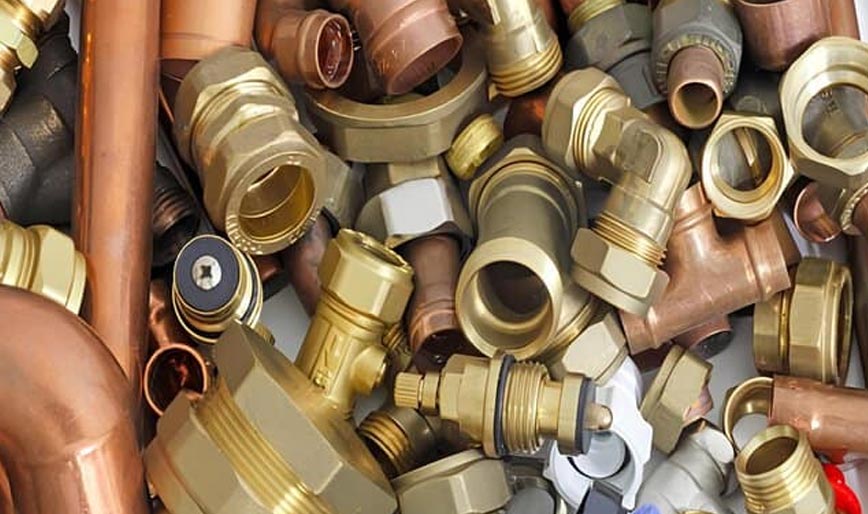
Flare fittings use a 45-degree flare on the end of the fitting and are often used in high-pressure hydraulic applications.
12. Tube Fittings
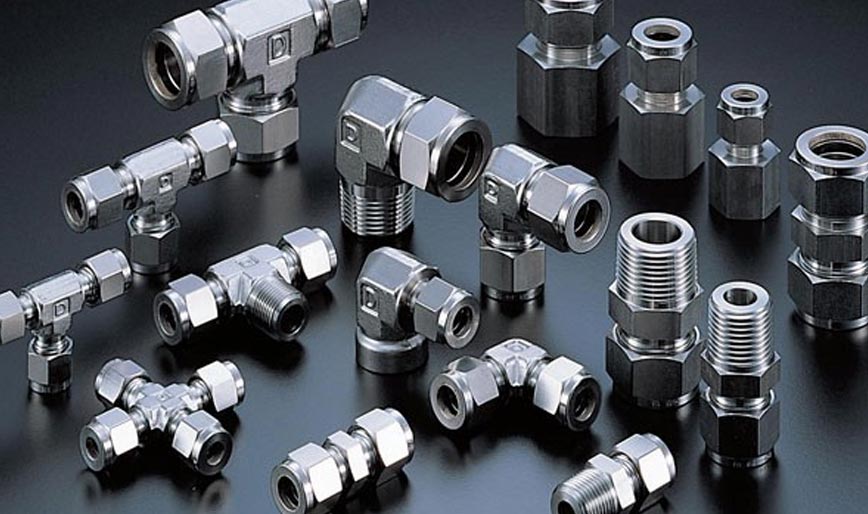
Tube fittings are used to connect and secure hydraulic tubes or pipes.
- Compression Tube Fittings: Secure tubes using compression nuts and ferrules.
- Push-on Tube Fittings: Allow for easy and quick connections by pushing the tube into the fitting.
13. Specialty Fittings
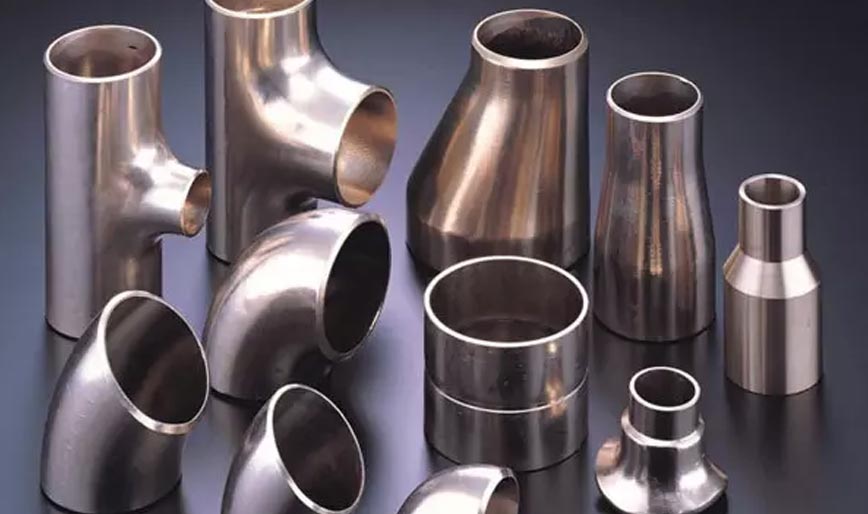
Specialty fittings are designed for unique applications or to handle specific requirements.
- Hydraulic Adaptors: Change the type or size of a hydraulic connection.
- Pressure Control Fittings: Used to regulate or control pressure within the hydraulic system.
Key Considerations for Hydraulic Fittings
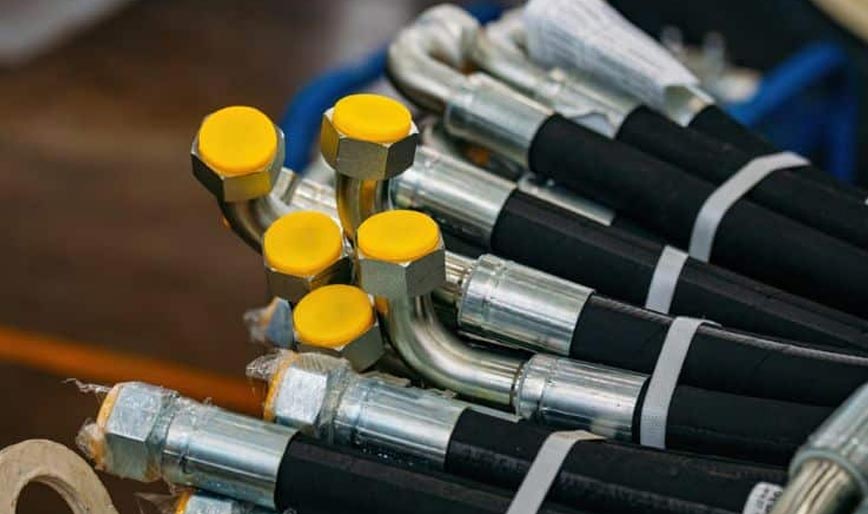
- Pressure Rating: Ensure the fitting can handle the pressure of the hydraulic system.
- Material Compatibility: Match the material of the fitting with the hydraulic fluid and operating environment.
- Temperature Range: Verify that the fitting can operate within the temperature range of the system.
- Sealing Mechanism: Choose the appropriate sealing method to prevent leaks.